Silicone rubber, a synthetic elastomer made of silicon, oxygen, carbon, and hydrogen, is known for its high flexibility and durability. Its journey began in the early twentieth century, and it developed significantly in the 1940s to meet the demand for materials that could endure extreme conditions, as opposed to traditional rubber.
This evolution led to the silicone rubber we know today, with a variety of formulations tailored to different applications. Its distinctive characteristics, such as resistance to extreme temperatures, UV light, and chemicals, as well as more effective electrical insulation, make it indispensable in a variety of businesses. Industries that include automotive, aerospace, electronics, and healthcare rely heavily on it for adaptability.
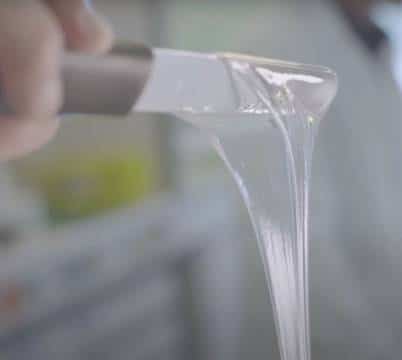
Silicone rubber has numerous applications, ranging from kitchenware and bakeware that can withstand high temperatures without degrading to medical devices that require a high level of biocompatibility and durability, demonstrating its critical role in modern material technology. In this blog, we will talk about silicone rubber so that you can gain a better understanding of it for your silicone rubber projects.
Composition and Types of Silicone Rubber
Silicone rubber’s chemical composition distinguishes it from conventional rubbers; it is composed of a silicon-oxygen chain with carbon and hydrogen side groups. This unique structure provides outstanding durability and flexibility, allowing it to withstand extreme temperatures and harsh chemical environments.
When we look at the various kinds of silicone rubber, we notice that each one is designed for a specific application. Liquid silicone rubber (LSR) is unique in its fluidity and ease of processing, making it ideal for complex and intricate molds used in medical devices, automotive parts, and baby products. LSR cures quickly under heat, allowing for rapid production cycles.
High-consistency rubber (HCR), also called high-temperature vulcanizing (HTV) silicone, has a much thicker, gum-like consistency. HCR’s strength makes it ideal for producing long-lasting products such as industrial seals, gaskets, and tubing. It requires high-temperature curing, which contributes to its outstanding thermal stability and strength.
Room temperature vulcanizing (RTV) silicone has particular benefits, as it cures at ambient temperatures without the need for additional heating.
RTV silicone is a versatile and user-friendly material that is widely used in sealants, adhesives, and mold-making processes. It can be separated into two types: one-part RTV, which cures with air moisture, and two-part RTV, and these cures when mixed with a catalyst, supply greater application and curing time flexibility.
Each type of silicone rubber, with its unique properties, serves in an assortment of industries, from automotive and aerospace to electronics and healthcare, demonstrating the material’s versatility and importance.
Properties and Advantages of Silicone Rubber
Silicone rubber boasts a set of physical and chemical properties that make it exceptionally versatile and durable. It is widely recognized for its excellent heat resistance, which can withstand temperatures that range from -55°C to more than 300°C, making it indispensable in applications that require exposure to extreme temperatures. In addition, silicone rubber retains its flexibility and strength across a wide temperature range, maintaining long-term durability in a variety of environments.
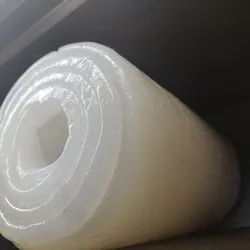
Chemically, silicone rubber is exceptionally stable, overcoming oxidation, ozone, ultraviolet light, and a broad spectrum of chemicals and solvents. This stability ensures that silicone products maintain their structural integrity and functionality over time, even under extreme circumstances.
The benefits of silicone rubber go beyond its physical and chemical properties. Its biocompatibility is critical, particularly for the medical field, where silicone is used in a wide range of applications such as implants, tubing, and medical devices. This compatibility with human tissue and body fluids, mixed with its sterility and non-reactivity, makes it a natural choice for healthcare applications.
Another significant benefit of silicone rubber is its resistance to weathering and UV light, which renders it ideal for use in outdoor applications where materials must withstand harsh environmental conditions without degrading. This includes sealants and coatings for buildings, automotive components, and outdoor electrical insulators.
Furthermore, silicone rubber has excellent electrical insulation properties, making it ideal for shielding cables, connectors, and various other electronic components. Its ability to prevent electrical conductance while withstanding high temperatures and environmental stress makes it highly useful in the electronics and electrical industries.
These combined properties and advantages indicate why silicone rubber is preferred over other materials in many applications, as it supplies a unique combination of durability, stability, and versatility that few other materials can match.
Manufacturing Process of Silicone Rubber
The silicone rubber manufacturing process consists of several key steps, beginning with polymerization, the foundational stage in which silicon and oxygen atoms combine to form long polymer chains. This reaction is catalyzed by metal salts and occurs under controlled conditions, which leads to the formation of the silicone rubber backbone structure.
After polymerization, the raw silicone base is blended with fillers and additives to enhance its properties. Fillers, such as fumed silica, are used to improve strength and elasticity, whereas additives may modify the color, increase flame retardance, or improve thermal conductivity. This mixing process is critical because it determines the rubber’s final characteristics and suitability for particular applications.
Molding and curing are the next actions in the process, which shape the silicone mixture into its final form. Molding can be done in an assortment of manners, including compression molding, transfer molding, and injection molding, depending on the complexity and properties of the final product. After molding, the silicone rubber treatment refers to a chemical process that cross-links the polymer chains, solidifying the material and giving it its final mechanical and thermal properties. Depending on the type of silicone rubber used, the curing process will either take place at room temperature or be accelerated by heat.
Quality control and testing are critical elements of the manufacturing process, ensuring that the silicone rubber meets strict standards and specifications. This involves rigorous testing for properties like tensile strength, elongation, tear resistance, and thermal stability. Additionally, quality checks are carried out to detect any flaws or inconsistencies in the material. Manufacturers can ensure that silicone rubber products are safe, reliable, and appropriate for their intended use by adhering to these meticulous processes, which assist in maintaining the material’s reputation for high performance and quality.
What Are Applications of Silicone Rubber?
Silicone rubber’s versatility has been shown across a wide range of applications, including industrial and automotive sectors, medical, consumer, and even aerospace industries. Silicone rubber is a valuable commodity in the industrial and automotive fields due to its durability and resistance to extreme temperatures and harsh conditions. It is commonly used to make gaskets, seals, hoses, and belts that can withstand high temperatures and harsh chemicals, ensuring in keeping performance in engines, machinery, and other automotive components.
Silicone rubber is used thoroughly in the medical and healthcare industries due to its biocompatibility, non-reactivity, and sterilizability. It is used in an extensive variety of products, including medical implants, surgical tools, tubing, and prostheses. Its flexibility and skin-friendly properties make it ideal for long-term medical applications. offers comfort and safety for patients.
Silicone rubber is a popular consumer product material due to its non-toxic, durable, and flexible attributes. Baking molds, spatulas, and food storage containers contain it, as do baby bottle nipples and pacifiers. Silicone’s excellent electrical insulation properties and heat resistance make it suitable for protective covers, keypads, and insulation materials, thus improving the durability and longevity of electronic devices.
Silicone rubber’s exceptional performance properties are also applicable to specialized applications in aerospace and engineering. It is used to make components like seals, gaskets, and insulation materials that can stand up to the harsh conditions of space and aviation environments, such as elevated temperatures, vacuum pressures, and exposure to aggressive chemicals. This material’s ability to maintain its properties under such harsh conditions makes it crucial in these high-tech, high-stakes fields.
Environmental Impact and Sustainability
The environmental impact of silicone rubber production and disposal is growing increasingly important. While silicone rubber is durable and resistant to many environmental factors, its production necessitates energy-intensive processes and the use of chemicals, which can contribute to environmental pollution if not properly managed. Disposal presents extra difficulties because silicone rubber does not biodegrade easily, which leads to potential accumulation in landfills.
However, there has been significant progress in the recycling and reusability of silicone rubber products. Silicone rubber can be ground down and reused as filler material in new silicone products, reducing waste and eliminating the requirement for raw materials. Efforts are additionally being undertaken to develop more efficient recycling processes that can break down silicone rubber into constituent materials for reuse, thus decreasing its negative environmental impact.
The silicone rubber industry is implementing more sustainable practices to reduce its environmental impact. This includes expanding energy efficiency in manufacturing processes, reducing waste and emissions, and investing in research to discover ecologically sound alternatives to traditional silicone rubber formulations. Companies are also focusing on the entire product lifecycle, from design to disposal, to ensure sustainable development. These efforts reflect the industry’s growing recognition of the need for sustainable materials and practices, to maintain the benefits of silicone rubber with the importance of environmental stewardship.
Silicone Rubber Manufacturer with Decade Experience
Silicone is a high-quality rubber polymer that may be suitable for your specific application. Contact us today to learn more about how we can assist you in making the best product selection.